Deming’s Process
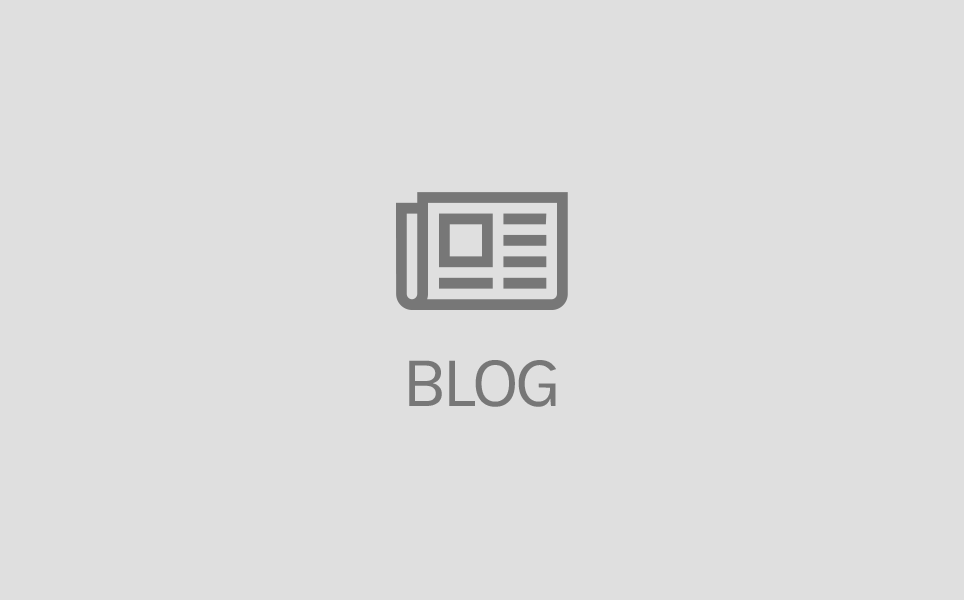
Deming’s Process
Deming’s Process, also known as the Plan-Do-Check-Act (PDCA) cycle, is a foundational framework for continuous improvement in quality management and process optimization. Developed by Dr. W. Edwards Deming, a pioneer in quality management, this iterative process is widely used in various industries to enhance efficiency, address issues, and achieve consistent results. The PDCA cycle is rooted in scientific methodology and is applicable to both organizational practices and individual projects.
1. Plan
The first step of Deming’s Process involves identifying a goal or a problem and developing a plan to achieve or address it. This stage requires a thorough understanding of the current situation, which involves collecting data, analyzing processes, and identifying areas for improvement. Key activities during the planning phase include:
- Defining Objectives: Establishing clear, measurable, and achievable goals.
- Analyzing Data: Examining existing processes to identify inefficiencies, gaps, or areas that need enhancement.
- Developing a Plan: Outlining steps, allocating resources, and setting timelines to achieve the defined objectives.
- Risk Assessment: Identifying potential challenges and devising mitigation strategies.
Effective planning lays the foundation for successful implementation and ensures that efforts are aligned with organizational goals.
2. Do
The second phase involves implementing the plan on a small scale to test its feasibility and effectiveness. This step allows organizations to validate their approach before full-scale deployment. Activities in this stage include:
- Executing the Plan: Implementing the proposed solution or improvement in a controlled environment.
- Monitoring Progress: Tracking key performance indicators (KPIs) and documenting results.
- Training and Communication: Ensuring that team members understand their roles and responsibilities in the implementation process.
The “Do” phase serves as a trial run to gather insights and refine the plan if necessary.
3. Check
In the third step, organizations evaluate the results of the implementation to determine whether the objectives were met. This phase involves comparing actual outcomes with the expected results and identifying discrepancies. Key activities include:
- Data Analysis: Reviewing performance data to assess the effectiveness of the implemented changes.
- Identifying Lessons Learned: Understanding what worked, what didn’t, and why.
- Feedback Collection: Engaging stakeholders to gather insights and suggestions for improvement.
The “Check” phase ensures that decisions are data-driven and that the process is on track to achieve the desired outcomes.
4. Act
The final phase focuses on standardizing successful changes and incorporating them into regular operations. If the implementation is deemed successful, the changes are adopted as the new standard. If not, the cycle begins again with revised strategies. Activities in this phase include:
- Standardizing Processes: Documenting best practices and integrating them into standard operating procedures (SOPs).
- Scaling Improvements: Expanding the implementation to other areas of the organization.
- Continuous Monitoring: Establishing mechanisms for ongoing evaluation and improvement.
By adopting the “Act” phase, organizations create a culture of continuous improvement and adaptability.
Benefits of Deming’s Process
Deming’s Process offers numerous advantages, including:
- Improved Quality: Enhances product and service quality through systematic evaluation and refinement.
- Increased Efficiency: Optimizes processes, reducing waste and resource consumption.
- Agility: Enables organizations to respond effectively to changes and challenges.
- Employee Engagement: Encourages collaboration and innovation among team members.
Conclusion
Deming’s Process is a powerful tool for fostering a culture of excellence and adaptability in organizations. By following the Plan-Do-Check-Act cycle, businesses can achieve sustainable improvements, drive innovation, and maintain a competitive edge in today’s dynamic landscape. Its iterative nature ensures that learning and growth are continuous, aligning processes with organizational goals and customer expectations.